Corrective and Preventive Action (CAPA): How to Implement
Introduction and Outcome
Corrective and Preventive Action (CAPA) process is a critical component of the quality management system in the pharmaceutical industry. It plays a vital role in using innovative skills and experience in identifying and addressing non-conformities, deviations and potential risks to ensure the safety, efficacy, cost-effectiveness and quality of pharmaceuticals. That is why I decided to share my skill-based knowledge on this topic. In this article, you will learn CAPA, CA (corrective action), PA (preventive action), the difference between CA and PA, case studies, the key aspects of CAPA, applications, advantages, and its importance in achieving continuous improvement and frequently asked questions on CAPA.
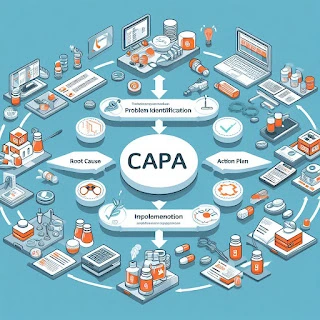
What is Corrective and Preventive Action (CAPA)?
The approach of using innovative skills and experience to tackle current issues and prevent future problems while considering quality, safety, efficacy and cost-effectiveness is called CAPA. This is the best tool to use the lessons learned smartly.
CAPA is a structured approach to investigating and resolving nonconformities and other undesirable situations in the pharmaceutical industry. It aims to eliminate the root cause of the problem and prevent its recurrence in the future. The level of effort, formality, and documentation involved in the investigation should be commensurate with the level of risk. CAPA management is an important component of the GLP and a key requirement of ICH Q10. It is also the Food and Drug Administration’s (FDA) requirement under FDA 21 CFR 820.100.
Mathematical representation of CAPA
CA + PA = CAPA
The two main functions of Corrective and Preventive Action (CAPA)
The following are the two main functions of CAPA:
- CA or Corrective Action &
- PA or Preventive Action
CA or Corrective Action
The aim of CA is to identify the root cause of the product and quality problems and take appropriate action against them. It includes:
- Review and definition of a problem
- Identification of the root cause of a problem
- Development of action plan for correction and prevention
- Implementation of the plan
- Evaluation of the plan efficiency
PA or Preventive Action
- Identification of potential problems
- Identification of root cause of the problem
- Development of recurrence prevention plan
- Implementation of the plan
Difference between corrective action and preventive action
Corrective Action (CA) | Preventive Action (PA) |
Reactive approach | Proactive approach |
It resolves an existing problem or prevents the recurrence of immediate problems e.g. audit findings and their compliance and Deficiency letters (DLs) and their response | The aim is to prevent problems before they arise (usually identified through risk assessment or trend analysis) and focus on reducing risks. e.g. Action to identify sources of DL to avoid DL in future |
The purpose of Corrective and Preventive Action (CAPA)
The purpose of CAPA is to collect information, analyze information, identify and investigate product and quality problems, and take appropriate and effective corrective and/or preventive action to prevent their recurrence
Typical examples of Corrective and Preventive Action (CAPA)
- Customer complains
- Deficiency letters (DLs)
- Failure of result
- Failure of experiments
- A lot of pharmaceutical product fails quality inspection due to a defect in its critical quality attributes (CQAs)
- SST failure during HPLC and GC analysis
The Role of CAPA in Other Industries
While CAPA is widely used in the pharmaceutical industry, it is also employed in other sectors such as electronics and automotive. These industries face similar challenges, including cost pressures, the need for reliability, and the demand for continuous improvement. The adoption of CAPA and other quality improvement methodologies, such as Six Sigma, has enabled these industries to achieve significant advancements in product quality and performance.
5-steps Corrective and Preventive Action (CAPA) Implementation Plan
The following are the 5-steps CAPA Implementation Plan:
- Identification: The initial phase of CAPA is called identification that collects the information from the event including the following elements:
- What is the event?
- What is involved in that event?
- Where is the event seen?
- When did the event happen?
- Evaluation: The second phase of the CAPA system is the evaluation phase, a very important phase as it also classifies what is, and is not, affected by the event such as:
- Is it affecting customer safety?
- Is it having an impact on regulatory documents?
- Is this affecting documentation or product design and materials or product performance?
- Has this event appeared before?
- Answers to all these questions provide the basis for the impact assessment of the event to assign a risk level to the event (high, medium, low).
- Investigation and Root Cause Determination: Once the event has been identified and evaluated, this can be investigated. So, the investigation is the third process in the CAPA system used to determine the root cause as well as identify corrective actions.
- Resolution Plan: The fourth step in the Corrective and Preventive Action (CAPA) system is appropriate Resolution Plans, having three main categories:
- Correction: A resolution to an existing problem usually occurs right after the event is identified in order to fix the immediate problem.
- Corrective Action: A resolution to prevent the reoccurrence of a problem that will address the root cause identified in the investigation.
- Preventive Action: A resolution to prevent the occurrence of a problem.
- Once the Resolution Plans are determined, they should be completed on time.
- Implementation: Implementation is the fifth step of the CAPA system where teamwork is needed depending on the scope of the resolutions. All resolution plans must be documented and these results must also be reviewed and approved by appropriate Quality Management to ensure compliance.
The final step of the CAPA system is the effectiveness check to make sure the action is appropriate for the root cause and prevents events in the future. Effectiveness checks involve the review of event data, conducting audits of affected products, materials, or equipment, etc
Case Study: Failure of Impurity profile analysis result in HPLC analysis
Example:
- API “Paracetamol” with the following impurity result was supplied to the customer
- Imp. A: NMT 0.06% (Limit NMT 0.15%), Any unknown impurity NMT 0.05% (Limit NMT:010%) and total impurity NMT 0.11% (Limit: NMT 0.30%)
- When the Paracetamol was analysed at the customer site it failed in impurity “A”. Customer analysis resulted in 0.30% (OOS) for impurity “A”
- Possible root causes:
- Method: The same method was used by the Customer and Manufacturer
- Column: The same make column was used by the Customer and Manufacturer
- Chromatographic condition: The same Chromatographic condition column was used by the Customer and Manufacturer
- Instrument: Same-make instruments were used by the Customer and the manufacturer
- Calibration: Calibrated instruments were used by both the Customer and the manufacturer
- Validation: Calibrated instruments were used by both the Customer and the manufacturer
- From the above details, it is clear that there was not any deviation in the analysis. Now the question is what is the root cause for variation in results for impurity “A”?
- Sample preparation procedure: while investigating the sample procedure it was observed that the sending lab was preparing the sample by sonication at a lower temperature (using the ice in the sonication bath). The customer also followed the same procedure except for the sonication temperature. Sonication was made at room temperature since temperature was not mentioned in the method monograph.
- When the sample was prepared at a low temperature (using the ice in a sonicator bath) the same result was obtained.
- Hence higher temperature was the root cause of the OOS result for impurity “A”.
- The sample preparation procedure was included in the method
The Desired State: Enhancing Product and Process Understanding
One of the primary goals of CAPA is to enhance product and process understanding. By identifying and addressing nonconformities and potential risks, CAPA methodology helps improve product and process performance, reliability, and quality. It enables organizations to gain insights into the root causes of issues and implement corrective and preventive actions to prevent their recurrence. This proactive approach promotes continuous improvement and ensures the delivery of safe and effective pharmaceutical products.
Elements or Components for an effective CAPA system
The following components play a crucial role in effective CAPA implementation:
- FMEA or Failure Mode and Effects Analysis: FMEA is an effective element of a proactive approach, that provides input for the CAPA activities
- APQP or Advanced Product Quality Planning: APQP is generally used in the automotive industry to drive quality improvement in mobility end products
- Strong Governance: A strong governance structure ensures proper scrutiny of corrective actions and timelines, thereby promoting accountability and responsibility throughout the organization.
- Management Review: Regular management reviews allow for the measurement of the achievement of quality system objectives and the assessment of performance indicators. This evaluation helps monitor the effectiveness of processes within the pharmaceutical quality system, including CAPA.
- Robust Business Processes: Well-defined and standardized business processes provide a foundation for effective CAPA implementation. They ensure consistency, efficiency, and transparency in addressing nonconformities and improving product and process performance.
- Standard Methodology: Having a standardized CAPA methodology helps streamline the investigation and resolution process. It provides a structured framework for identifying root causes, implementing corrective and preventive actions, and evaluating their effectiveness.
- Information System: An integrated information system facilitates the capture, analysis, and reporting of CAPA-related data. It enables organizations to track and monitor the progress of CAPAs, identify trends, and generate actionable insights.
- Effective Training: Comprehensive training programs ensure that employees understand the CAPA process and their roles and responsibilities in its implementation. Training helps build a culture of quality and continuous improvement within the organization.
Lessons Learned from CAPA Implementation
Implementing a successful CAPA system requires organizations to learn from their experiences and continuously improve their processes. Some of the key lessons learned from CAPA implementation include:
- Avoid Overwhelming the System: The sheer number of CAPAs can overwhelm an organization. Prioritizing and focusing on critical issues is essential to ensure effective and timely resolution of nonconformities.
- Set Realistic Timelines: Artificially imposed timelines can lead to rushed investigations and inadequate root cause analysis. Setting realistic timelines allows for thorough investigations and the identification of sustainable corrective and preventive actions.
- Choose the Right Metrics: Selecting the appropriate metrics to monitor CAPA performance is crucial. It is important to focus on a few critical metrics that provide meaningful insights into the effectiveness of the CAPA system and drive the right behaviours.
- Strong Governance and Oversight: Establishing strong governance and oversight mechanisms ensures that CAPA processes are adequately reviewed, monitored, and improved. Regular management reviews and a commitment to quality are crucial to the success of the CAPA system.
The Future of Corrective and Preventive Action (CAPA) in the Pharmaceutical Industry
As the pharmaceutical industry continues to evolve, the CAPA process is expected to evolve as well. Some future trends and developments include:
- Non-Exception Type Data: CAPAs will increasingly be based on non-exception type data, such as data trending and holistic data reviews. This shift will enable organizations to identify potential issues proactively and implement preventive actions.
- Early Implementation in the Development Process: CAPA will be implemented earlier in the product development process, allowing for early detection and resolution of nonconformities and risks. This proactive approach will help prevent significant problems and improve overall product quality.
- Industry and Regulatory Surveillance: Organizations will leverage industry and regulatory surveillance to identify emerging trends and potential risks. This proactive monitoring will enable timely CAPA implementation and ensure compliance with evolving regulatory requirements.
- Cost of Quality Model: The adoption of cost of quality models will help organizations quantify the financial impact of nonconformities and the benefits of implementing CAPAs. This approach will facilitate resource allocation and investment decisions related to CAPA activities.
Advantages of Corrective and Preventive Action (CAPA)
- Better customer satisfaction, safety and security
- Improved productivity and better product quality
- Lower cost of regulatory non-compliance (fines, penalties)
- Audit compliance
Importance of CAPA in QMS (Quality management system)
Corrective and preventive actions (CAPAs) are important in a quality management system (QMS), which ensures continuous improvement and adherence to quality standards.
Conclusion
CAPA is a structured and defined approach that empowers organizations to address various problems and prevent their recurrence through a comprehensive approach to quality management and continuous improvement. It is a versatile tool that can be applied across a variety of industries and provides organizations with the means to identify, investigate, and effectively resolve issues.
CAPA is a vital tool in the pharmaceutical industry, enabling organizations to identify and address nonconformities, deviations, and potential risks. It promotes continuous improvement, enhances product and process understanding, and ensures the delivery of safe and effective pharmaceutical products. By implementing a robust CAPA system and learning from past experiences, organizations can achieve regulatory compliance, improve product quality, and safeguard patient safety. This is all about this post.
I hope this article has helped you understand CAPA and its importance. Now you can independently plan and implement CAPA.
FAQS
What is the CAPA?
The approach of using innovative skills and experience to tackle current issues and prevent future problems while considering quality, safety, efficacy and cost-effectiveness is called CAPA. This is the best tool to use the lessons learned smartly.
What is the role of CAPA in the industries?
The role of CAPA in the industries is to collect information, analyze information, identify and investigate product and quality problems, and take appropriate and effective corrective and/or preventive action to prevent their recurrence.
How CAPA is implemented?
The CAPA is implemented in 5 stages: Identification, Evaluation, Investigation and Root Cause Determination, Resolution Plan, and Implementation
What are the advantages of CAPA implementation?
There are several advantages of CAPA implementation such as better customer satisfaction, safety and security, improved productivity and better product quality, lower cost of regulatory non-compliance (fines, penalties), and audit compliance.
What is CAPA in quality control?
Corrective and preventive actions (CAPAs) are important in a quality management system (QMS), which ensures continuous improvement and adherence to quality standards.
What are the four stages of CAPA?
Identification, Evaluation, Investigation and Root Cause Determination, Resolution Plan:, and Implementation are main stages of CAPA.
What is the CAPA principle/ rule?
CAPA is a structured approach to investigating and resolving nonconformities and other undesirable situations in the pharmaceutical industry. It aims to eliminate the root cause of the problem and prevent its recurrence in the future
What are the two types of CAPA?
Two types of CAPA are CA or Corrective Action & PA or Preventive Action.
What is CAPA as per 21 CFR?
The CAPA is under under FDA 21 CFR 820.100
How many steps are there in CAPA?
There are five steps in CAPA; Identification, Evaluation, Investigation and Root Cause Determination, Resolution Plan:, and Implementation
What is CAPA life cycle?
The CAPA process follows the Plan-Do-Check-Act (PDCA) cycle to resolve unexpected events.
What are the elements of CAPA?
FMEA or Failure Mode and Effects Analysis and APQP or Advanced Product Quality Planning are the elements of CAPA
What is KPI in CAPA?
KPIs (Key performance indicators) in CAPA include; Time to resolution: Measure the time from problem identification to successful resolution. Number of Open CAPAs: Track the number of CAPAs running at any time.
How to write a CAPA plan?
Identification, Evaluation, Investigation and Root Cause Determination, Resolution Plan:, and Implementation are the main steps of CAPA plan
What is CAPA sop?
The SOP which deals about the implantation of CAPA is called CAPA SOP
How to fill CAPA format?
The CAPA format is filled into 6 steps Identification, Evaluation, Investigation and Root Cause Determination, Resolution Plan, Implementation and approval
What is the purpose of CAPA?
The purpose of CAPA in the industries is to collect information, analyze information, identify and investigate product and quality problems, and take appropriate and effective corrective and/or preventive action to prevent their recurrence.
How do you write a CAPA report?
The CAPAreport is written into 6 steps Identification, Evaluation, Investigation and Root Cause Determination, Resolution Plan, Implementation and approval
References
Abbreviations
- CAPA:
- RCA:
- FMEA:
- CQ: Cost of Quality
- QMS:
- CA: Corrective action
- PA: Preventive action
- SST: System suitability test
- HPLC: High performance liquid chromatography
- GC: Gas chromatography
It is a good topic.