What Safety Precautions Do Pharma Factories Take To Prevent Explosions
Safety is paramount, especially when handling volatile chemicals and substances that can pose explosion risks in pharmaceutical development. While the image of a clean lab may come to mind, behind the scenes, there are rigorous protocols and engineering controls that ensure both product quality and worker safety. Here’s how pharma factories prevent explosions and maintain a safe working environment.
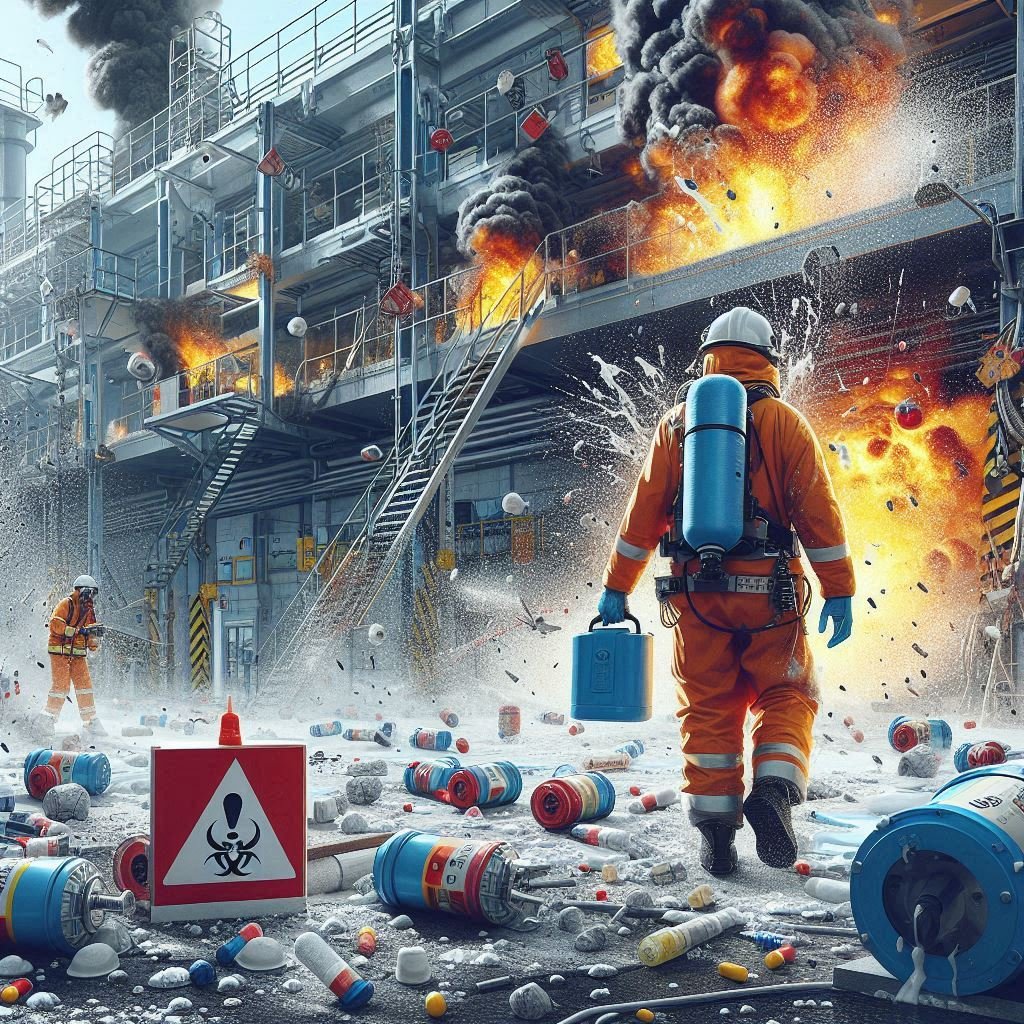
What Safety Precautions Do Pharma Factories Take To Prevent Explosions
Here’s how pharma factories prevent explosions and maintain a safe working environment:
1. Control of Flammable Vapours and Dust
Many pharmaceutical ingredients are in powder or solvent form. Fine powders can become airborne and combustible, while solvents often release flammable vapours. To prevent buildup:
- Factories use dust collection systems and maintain clean environments.
- Flammable solvents are stored in sealed containers and ventilated areas.
- Vapour detection systems are installed to monitor concentrations in the air.
2. Explosion-Proof Equipment
Equipment used in high-risk areas is specially designed to prevent ignition. This includes:
- Intrinsically safe electrical components.
- Non-sparking tools and anti-static flooring.
- Enclosed process systems that isolate reactive chemicals.
3. Static Electricity Management
Static discharge can be a major ignition source in dry environments. To manage this:
- Machines and containers are grounded and bonded.
- Humidity levels are monitored and controlled.
- Workers wear anti-static clothing and footwear.
4. Proper Chemical Handling and Storage
All chemicals are labelled, stored, and transported according to strict guidelines:
- Incompatible substances are separated.
- Storage areas are temperature-controlled and ventilated.
- Material Safety Data Sheets (MSDS) are readily accessible.
5. Ventilation and Airflow Control
Well-designed airflow systems dilute and remove hazardous vapours or dust:
- Fume hoods, scrubbers, and HEPA filters are commonly used.
- Cleanroom environments use controlled airflows to minimise contamination and risks.
6. Training and Emergency Preparedness
Even the best equipment needs well-trained operators. Pharma facilities provide:
- Regular safety training and drills.
- Clear emergency shutdown procedures.
- Access to personal protective equipment (PPE) and fire suppression systems.
Conclusion
Preventing explosions in pharmaceutical factories isn’t just about compliance—it’s about protecting lives, infrastructure, and the integrity of medicines we depend on. Through a combination of advanced technology, strict protocols, and a culture of safety, the industry works proactively to keep every process as safe as it is effective.
Related:
FAQs: Explosion Prevention in Pharmaceutical Development
Why are pharmaceutical factories at risk of explosions?
Pharma factories often handle flammable solvents, combustible dusts, and reactive chemicals. Without proper controls, these materials can ignite and cause fires or explosions, especially during mixing, drying, or transfer processes.
What types of equipment are considered explosion-proof?
Explosion-proof equipment includes motors, lighting, electrical panels, and instruments designed to contain any ignition within the device. These are certified for use in hazardous areas where flammable gases or dust may be presen
How do factories control static electricity?
Static is managed by grounding and bonding all conductive equipment, maintaining optimal humidity, using anti-static flooring and clothing, and ensuring proper material handling practices to prevent static buildup.
What is a dust explosion, and how is it prevented?
A dust explosion occurs when fine particles suspended in air ignite. To prevent this, pharma factories install dust collection systems, use explosion vents, maintain clean workspaces, and control ignition sources.
Are all solvents in pharmaceutical manufacturing explosive?
Not all, but many solvents like ethanol, acetone, and isopropanol are highly flammable. These require controlled environments, proper ventilation, and safe handling procedures to reduce explosion risks.
How often are safety systems and procedures reviewed?
Most facilities conduct regular safety audits, hazard analyses (e.g., HAZOP studies), and emergency drills. Critical systems are reviewed at least annually or after any incident or process change
What role does employee training play in explosion prevention?
Training is crucial. Employees must understand the hazards, know how to handle materials safely, recognise signs of danger, and respond quickly in emergencies. Ongoing training ensures safety practices stay top of mind
Further Reading